robincnn
Well-Known Member
Well ,yes ..
I agree ..
I prefer large diameter fans with low rpm and low power dissipation.
But the heat sink has to be chosen in accordance with that kind of fans ..
Meaning thick and short fins ,with quite a space between them ,in order to minimise
flow resistance (thus pressure drop ) ,as large rotor /low rpm /low power fans tend to stall ,
under high flow resistance .
This kind of active cooling is way different in many ways ,than HSF systems of
small diameter fans with high rpm ...
Those fans work best with another design of heat sinks ...
Regarding the mass and size of the heat sink ,the large diameter /low rpm HSF system ,
falls somewhere in between passive cooling and small diameter / high rpm active HSF system .
The former needs large size/mass heatsink ,while the latter utilises smallest mass/size heat sink possible ...
The former is totally quite ,the latter quite noisy ...
The former is fail-proof ,the latter if the fan fails ...bye-bye COBs ...
My taste ,is somewhere in between ...
I agree the heatsink choice is important along with the fan size and type. Fan blades design and static pressure also important.
A fan with high static pressure may do better under high flow resistance.
And a fan with higher CFM but lower static pressure may do better under low flow resistance.
Seems you prefer an active cooled design with heatsink design such that NO 'Bye bye COB' if the fan fails. Thick short fins with wide space in between or
Medium size Pin type with pins length cut to 30-40 mm and a fan should work well in active cooling and allow sufficient passive cooling if fan fails.
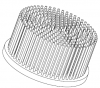