robincnn
Well-Known Member
yes that is TIM all over LES. I have cleaned and re-applied thermal compound on this one over a dozen times trying to figure out what is the best way and how much to apply. . It got I actually cleaned it with alcohol and cotton swabs before taking a pic. It was real bad earlierIs that TIM all over the cob? If it is..whatever it is..its good to have iso alcohol around and paper towels to get them shiny clean before using.

i will make a vero 29 stencil to TIM application to keep it clean and even
The thermocouple wire is too exposed for me too..be good to snip the wire shorter so no exposed wire near terminals.
I use kapton on the thermocouple but its not easy to get it just right that way..need to get the wire to naturally press against the test spot and kapton tape it in place..your way is more secure though. Tape would be a no go since the terminals are exposed..
Time to toss the vero unfortunately...regardless of what its running at..
just some stuff to ponder...not trying to be critical. I tossed a cxa that the solder pad seperated from board while trying to use the ledil clamp.
Good luck and keep at it...hopefully sds can give you some good info
You mentioned snip the wire. Do you mean I can cut the thermocouple junction shorter ?
Will try with kapton tape next time and put a little TIM on junction.
Thanks for the feedback. I have tortured me first vero enough and it still works. I will keep this one for experiments.
i read the AN30 and saw the bridgelux video a couple of times. They say 30 guage or higher. 36 preferred. I bought this one and it is way to big. Photo attached...notes on thermocouple way...
http://www.bridgelux.com/sites/defa...30-Thermal-Management-of-Vero-LED-Modules.pdf
page 26 and 27
Special care is required when measuring the Tc to ensure an accurate measurement.
As mentioned above, a Tc measurement location is provided on the top side of the Vero module for easy access in a location which Bridgelux has defined near the Light Emitting Surface (LES) and is intended for measuring the temperature with a fine gage thermocouple.
This measurement location is identified in the mechanical section in the Vero LED module datasheets.
The thermocouple attach area is large enough to accommodate a 30 gauge thermocouple, but a smaller gage such as 36 gauge is recommended for ease of attachment and better accuracy,
see figure 9 below which shows the attachment location.
The following approach is recommended to minimize measurement errors for attaching the thermocouple
to the case temperature measurement point of the Vero LED Modules.
A microscope will aid in the installation of the thermocouple detailed in the next steps
View attachment 3434228
View attachment 3434229
View attachment 3434230
...add the vid....
https://www.rollitup.org/t/v-series-tetras.858075/page-15#post-11567816
pd... maybe add the reflowoven shield wiith an arduino... and maybe add an diy microscope with a old web cam....to make pics or vids with the process...or looking tricomas or leaves or insects...with a ring of leds for better illumination...
saludos
http://www.ebay.com/itm/400542887700?_trksid=p2057872.m2749.l2649&ssPageName=STRK:MEBIDX:IT
Not sure where i can get a 30 to 36 gauge K type thermocouple..
Thanks for the photos. The thermocouple came out today. I will definitely use a kapton for strain relief next time.
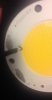