Bumping Spheda
Well-Known Member
Idk why I don't take pictures while in the process, I just get in the zone and go too fast. BUT, I can explain the process and give you tips on disassembling a 9.5W Cree bulb if you're interested. I plan to mount the metal core PCB onto an Aluminum heat sink and using this in my veg tent.
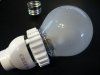
So this what we're talking about (yours hasn't been taken apart... yet).
http://www.designingwithleds.com/cree-60w-led-replacement-bulb-review-and-tear-down/
I got this little tip here, but basically, preheat your oven to 200F and grab yourself some thick leather gloves to protect your hands. Place bulb in oven on a cookie sheet for 20 minutes. Take bulb out and grab the heat sink/base in one hand, and the silicone covered glass in the other. Now be careful because when I removed mine I pulled too hard and the heated glass sheared the protective covers off two of my LED's (you'll see in late photos). They still work, but Idk if I lost lumens on those two, or? So, what you wanna do, is pry the glass off (not twist), but just enough to crack the glue so that you can slowly pull the glass away from the rest of the assembly in a controlled manner.
This is what you should see, but of course your LED's and PCB will still be in place. Pull the LED's off at this point and place somewhere safe, they're only being held on by friction. Careful, the metal may still be warm. Now, to get the heat sink separated from the base to get access to the driver there are three tabs (two have red arrows indicating their locations in the picture above), however, the glue that was holding the glass on is in the way (last red arrow in picture above). Get a knife and chip that stuff off/away from the clips. Once you do this you should be able to use the knife to pry those plastic tabs outwards and pull the heat sink off.
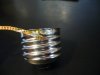
Look at the base. There should be a little wire hung outside. I took desoldering braid and desoldered the wire so I could pull the base off. Pretty easy, not much is holding it on so you should be able to do this by hand.
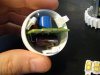
Now you can pull the driver out. On both the driver and the LED PCB there are designated tabs for (+) and (-) so you can't mess it up.
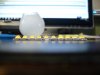
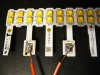
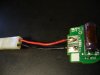
Get a set of needle nose pliers (or two) and bend the PCB as flat as possible. Notice the two LED's second from the left in the second pic? Hum, sliced those suckers right off. :3 Anyway, I soldered wire with molex plugs onto each set of tabs so I can quickly (dis)connect the heat sink/LED's from the driver if I ever have to. Both the driver and LED PCB's have (+) and (-) clearly labeled so it'd be hard to mess up. I'm going to find a power cord for the driver, solder that on (no polarity, remember) and then spray a couple coats of PlastiDip over the driver. I really don't want things shorting out on me at any time and fudging things up. If you have a small box that it would fit in (a LARGE pill case, maybe?) I say drill holes in it, feed all the wires through and solder that puppy up.
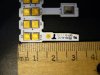
What size heat sink should I buy? Well, it measures ~65mm x ~32mm, so something larger than that I'd say.
http://cgi.ebay.com/ws/eBayISAPI.dll?ViewItem&item=200800824597&ssPageName=ADME:L:OC:US:3160
That's what I just bought. I was waiting to measure the PCB before I bought anything so there wasn't a face palm moment later on. Yeah, it's on the large side, I could have saved a few bucks, I know. I liked the height of the fins, and... Idk. Buy whatever looks good to you. Judging by the size of the stock heat sink if the new heat sink is large enough for the LED PCB to fit completely on it should be large enough.
Well that wraps things up pretty much. Waiting for the heat sink and I'll probably have an update for you guys on this build within the next week or so. Hope you enjoyed it.
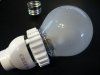
So this what we're talking about (yours hasn't been taken apart... yet).
http://www.designingwithleds.com/cree-60w-led-replacement-bulb-review-and-tear-down/
I got this little tip here, but basically, preheat your oven to 200F and grab yourself some thick leather gloves to protect your hands. Place bulb in oven on a cookie sheet for 20 minutes. Take bulb out and grab the heat sink/base in one hand, and the silicone covered glass in the other. Now be careful because when I removed mine I pulled too hard and the heated glass sheared the protective covers off two of my LED's (you'll see in late photos). They still work, but Idk if I lost lumens on those two, or? So, what you wanna do, is pry the glass off (not twist), but just enough to crack the glue so that you can slowly pull the glass away from the rest of the assembly in a controlled manner.
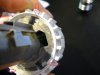
This is what you should see, but of course your LED's and PCB will still be in place. Pull the LED's off at this point and place somewhere safe, they're only being held on by friction. Careful, the metal may still be warm. Now, to get the heat sink separated from the base to get access to the driver there are three tabs (two have red arrows indicating their locations in the picture above), however, the glue that was holding the glass on is in the way (last red arrow in picture above). Get a knife and chip that stuff off/away from the clips. Once you do this you should be able to use the knife to pry those plastic tabs outwards and pull the heat sink off.
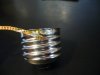
Look at the base. There should be a little wire hung outside. I took desoldering braid and desoldered the wire so I could pull the base off. Pretty easy, not much is holding it on so you should be able to do this by hand.
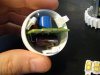
Now you can pull the driver out. On both the driver and the LED PCB there are designated tabs for (+) and (-) so you can't mess it up.
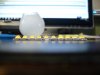
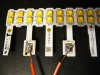
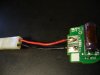
Get a set of needle nose pliers (or two) and bend the PCB as flat as possible. Notice the two LED's second from the left in the second pic? Hum, sliced those suckers right off. :3 Anyway, I soldered wire with molex plugs onto each set of tabs so I can quickly (dis)connect the heat sink/LED's from the driver if I ever have to. Both the driver and LED PCB's have (+) and (-) clearly labeled so it'd be hard to mess up. I'm going to find a power cord for the driver, solder that on (no polarity, remember) and then spray a couple coats of PlastiDip over the driver. I really don't want things shorting out on me at any time and fudging things up. If you have a small box that it would fit in (a LARGE pill case, maybe?) I say drill holes in it, feed all the wires through and solder that puppy up.
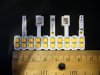
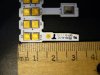
What size heat sink should I buy? Well, it measures ~65mm x ~32mm, so something larger than that I'd say.
http://cgi.ebay.com/ws/eBayISAPI.dll?ViewItem&item=200800824597&ssPageName=ADME:L:OC:US:3160
That's what I just bought. I was waiting to measure the PCB before I bought anything so there wasn't a face palm moment later on. Yeah, it's on the large side, I could have saved a few bucks, I know. I liked the height of the fins, and... Idk. Buy whatever looks good to you. Judging by the size of the stock heat sink if the new heat sink is large enough for the LED PCB to fit completely on it should be large enough.
Well that wraps things up pretty much. Waiting for the heat sink and I'll probably have an update for you guys on this build within the next week or so. Hope you enjoyed it.