stardustsailor
Well-Known Member
Back to the heatsink ...
Drilling time ...
But before that some "careful" drawing ..
Remember one the 'gold rules ' of an efficient HSF cooling system ?
"The coldest part of air ,to the hottest part of heatsink "

Or vice versa ..
The hottest part of heatsink 's fins ,underneath the coolest part of fan blown air stream ....
Wiring ,this time ,will be done through the heatsink ...
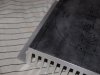
Cheers .
Drilling time ...
But before that some "careful" drawing ..
Remember one the 'gold rules ' of an efficient HSF cooling system ?
"The coldest part of air ,to the hottest part of heatsink "

Or vice versa ..
The hottest part of heatsink 's fins ,underneath the coolest part of fan blown air stream ....
Wiring ,this time ,will be done through the heatsink ...
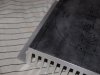
Cheers .