Pyewacket
Well-Known Member
Inspired by Fadedawg's Terpenator models and write-ups -- I have found myself wanting to try my hand at a VERY low budget strip-down version -- oil extractor. Absolutely nothing fancy about this, and it is very much specific to what I have been making (winterized BHO shatter). In fact (if this works--and it is a big IF) the only way to reclaim the oil from the collection vessel will be to dissolve it in ethanol and pour it it out -- as opposed to scraping it.
Here are some thoughts and concerns:
Copper - Yes I am using copper for the evacuation chamber. I am comfortable with using copper in distillation equipment construction. Copper is used world-wide in a variety of distillation apparatuses...it is used in many homes/municipalities for potable water -- it is even common in cooking-ware. Some folks are concerned with copper patina contaminating the product -- properly cared for copper will impart no contamination.
Pressure -- I have made similar vessels, and I have pressure tested them well above the PSIg/temp evaporation pressure of butane. I will be pressure testing these vessels once I receive my valves.
Stainless solder integrity. Over the years I have soft soldered stainless to copper and stainless to stainless with very good results. Using the correct flux and solder is imperative, but if one takes his time...the join is amazingly strong.
Cleaning without the ability to fully disassemble. One of the advantages of working with these two solvents is that they can naturally strip and remove most of what needs to be cleaned. Most homedistillers have boilers that are fully enclosed (except for still head path). Additional cleaning will be done with abrasive raschig rings that can be swirled inside the vessels...for extra cleaning.
Cost. I still need to purchase my valves and connection hose, but what you see in the photos is roughly $20 worth of materials. My guess, $65-$75.
Some photos of what I have thus far:
The copper evacuation tube is soldered onto a soldered sealed vessel. The vessel is two medium thickness stainless steel bowls soldered together. The vessel on the right will be the butane storage vessel.
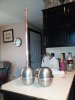
This is the top of the evacuation tube. I will solder a 1/4" stainless valve suitable NPT fitting to receive the stainless valve for this evacuation tube. The two threaded fittings will be sealed with gas appropriate Teflon tape.
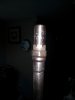
To construct the vessel. Both lips are tined(pre-solder coated). A torch applies the heat, and the two halves are melted together. I used these clasps to apply downward pressure as I am heating the perimeter to melt them together.
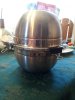
The above step does a wonderful job of fusing. But to ensure a good seal...You need to back fill with solder. This takes a while. When finished, the joint must be cleaned with a grinder. This will reveal any air-pockets, and you will have to re-solder that spot.
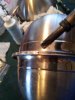
If done correctly, you get a nice THICK bead of fill...that is remarkable strong. This is the butane storage vessel. I will need to solder a valve into the vessel once they arrive.
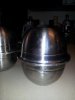
This is a passive extractor (no vacuuming device). Meaning, temperature variants will create vacuum/suction pressure and allow the butane to flow through the system. It is very much a distillation process when extracting the butane into to the storage container -- leaving behind the THC oil in the first container -- capturing the solvent in the storage container. The storage container will be stored in the freezer...at this temperature the PSIg should be nearly zero.
This is where I am in the process. Not sure anyone cares, but I will add additional information as I finish this build. Once I have the valves installed, I will try to do a better job of explaining the flow of butane and the way this mess should work.
Here are some thoughts and concerns:
Copper - Yes I am using copper for the evacuation chamber. I am comfortable with using copper in distillation equipment construction. Copper is used world-wide in a variety of distillation apparatuses...it is used in many homes/municipalities for potable water -- it is even common in cooking-ware. Some folks are concerned with copper patina contaminating the product -- properly cared for copper will impart no contamination.
Pressure -- I have made similar vessels, and I have pressure tested them well above the PSIg/temp evaporation pressure of butane. I will be pressure testing these vessels once I receive my valves.
Stainless solder integrity. Over the years I have soft soldered stainless to copper and stainless to stainless with very good results. Using the correct flux and solder is imperative, but if one takes his time...the join is amazingly strong.
Cleaning without the ability to fully disassemble. One of the advantages of working with these two solvents is that they can naturally strip and remove most of what needs to be cleaned. Most homedistillers have boilers that are fully enclosed (except for still head path). Additional cleaning will be done with abrasive raschig rings that can be swirled inside the vessels...for extra cleaning.
Cost. I still need to purchase my valves and connection hose, but what you see in the photos is roughly $20 worth of materials. My guess, $65-$75.
Some photos of what I have thus far:
The copper evacuation tube is soldered onto a soldered sealed vessel. The vessel is two medium thickness stainless steel bowls soldered together. The vessel on the right will be the butane storage vessel.
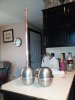
This is the top of the evacuation tube. I will solder a 1/4" stainless valve suitable NPT fitting to receive the stainless valve for this evacuation tube. The two threaded fittings will be sealed with gas appropriate Teflon tape.
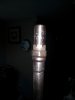
To construct the vessel. Both lips are tined(pre-solder coated). A torch applies the heat, and the two halves are melted together. I used these clasps to apply downward pressure as I am heating the perimeter to melt them together.
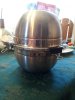
The above step does a wonderful job of fusing. But to ensure a good seal...You need to back fill with solder. This takes a while. When finished, the joint must be cleaned with a grinder. This will reveal any air-pockets, and you will have to re-solder that spot.
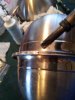
If done correctly, you get a nice THICK bead of fill...that is remarkable strong. This is the butane storage vessel. I will need to solder a valve into the vessel once they arrive.
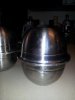
This is a passive extractor (no vacuuming device). Meaning, temperature variants will create vacuum/suction pressure and allow the butane to flow through the system. It is very much a distillation process when extracting the butane into to the storage container -- leaving behind the THC oil in the first container -- capturing the solvent in the storage container. The storage container will be stored in the freezer...at this temperature the PSIg should be nearly zero.
This is where I am in the process. Not sure anyone cares, but I will add additional information as I finish this build. Once I have the valves installed, I will try to do a better job of explaining the flow of butane and the way this mess should work.