bassclef
Active Member
Have a micro cab? Thinking of building one? Frustrated with hot, bulky CFL lighting? Confused by inferior, expensive LED lamps? You've come to the right place.
DIY LED lights are perfect for space-restricted micro cabs. They're small, customizable, efficient, and (best of all) COOL. No more overheating PC cases!
I made this light with leftover supplies from a much larger light. It was fun to assemble and took about an afternoon. The design is meant to be as cheap and efficient as possible. This light can be used standalone for micro grows, for vegetative and/or mother cabs, or to supplement specific areas of a larger garden. Build the light as pictured, or expand it over a larger heatsink. The basic concept is the same whether you have 4 or 40 LEDs.
Before embarking on this adventure, be advised that it helps to have soldering experience BUT it's not necessary. A beginner should watch a couple youtube tutorials, then practice soldering wires together until they get the hang of it. A basic knowledge of electrical concepts is helpful as well, although if you've ever wired a DC fan to a wall-wart it's really not much more complicated than that.
Without further ado, let's get started. Here we have our supplies (counter clockwise from top left):
Osram Golden Dragon Plus LEDs 660nm red and 6500K bright white (~$5-$7 each from Mouser, more if you buy in bulk). These have a nice, wide coverage angle (170 degrees) and are easy to solder. You can get the plants nice and close without burning them. For a flower light, 3500K warm whites should be used in place of 6500K; also add a royal blue if you have space. For flowering I use a ratio of 5R:2W:1B.
Pre-stripped wires (from Rapid LED)
Molex connector that I'll cut in half to use for the plugs (also from Rapid LED)
Meanwell LPC-35-700 driver Readily available and cheap (~$16) that will drive up to 48V of LEDs at 700mA. Features short circuit and overcurrent protection in the form of a xener diode. Basically they're rock-solid. One of these will drive up to 12-15 LEDs on average.
Wakefield thermal pads, 173-7 series (also available from Mouser, very cheap, very thin @ .007", great thermal conductivity)
Copper CPU heatsink Any finned heatsink (aluminum or copper) will do; check ebay for a wide variety of cheap ones. This one is just an old one I had lying around. The bigger the light, the bigger the heatsink needs to be. A good rule of thumb is 9 square inches of heatsink surface area per watt for actively cooled lights; and 27 square inches for passively cooled. If your heatsink is too small, the area beneath the LED will get too hot, and your light will be less efficient.
Kapton tape to isolate the leads from the heatsink (couple bucks from dealextreme)
Thermal adhesive 2 part epoxy, non-conductive. I use Arctic Silver.
Multimeter for testing
Soldering iron & solder
Scissors, exacto knife (or razor) and tweezers
Extension cord (not pictured) You'll need this for the plug, so you can wire up the AC end of the driver.
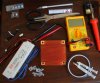
First we pre-tin the leads on all the LEDs and wires. This ensures a solid electrical path and makes connecting them to the wires much easier once they're mounted to the heatsink. Simply melt a bit of solder on the end of the gun and touch each lead for 3-5 seconds, or until the solder transfers over and becomes shiny. Go slow and be careful not to burn the plastic housing. After you tin, GENTLY bend the leads upwards a bit. This gives us more room to press the LED down onto the thermal pad in the next step. Pre-tin your wires as well.

Next, cut the thermal pads to size and glue them to the bottom of the heatsink with the thermal paste. Ideally they should be slightly larger than the metal slug at the bottom of the LED. Apply pressure while the epoxy sets up; about 5 minutes is enough. Once it's dry you can trim off the excess goo with a razor.
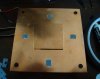
Put a small piece of Kapton tape on each side of the thermal pad. This electrically isolates the leads from the heatsink.
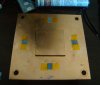
Dab a bit of epoxy on the top of the pad and attach the LED. Again, apply gentle yet firm pressure to the sides of the LED while it dries (about 5 minutes). If a LED comes off, scrape the dry glue from the bottom and re-apply. If the epoxy is stubborn, clean the area with alcohol and start over. Attach each LED with the cathode (negative) side facing the same way. See that little dot to the right of the light? That's the cathode side.
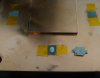
Once you've attached everything let it sit for awhile as the epoxy sets up. Within an hour or two the epoxy will be 90% hard and you won't be able to remove the LED without risking damage to it.
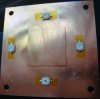
Almost there! Now we need to wire them together in series. Remember back in high school learning about AC/DC current, and parallel and series circuits? Well, LED lights are simply a series DC circuit. This is why it's important to keep the cathode facing the same direction. Since we pre-tinned all of our leads, this should be easy. Bend the wires where you want them to go, and touch the soldering iron to the leads, connecting positive to negative all the way around. They should adhere within seconds. Again, this is where your super excellent soldering skills will come in handy, so practice up a bit! As you can see, mine are not perfect, but it's good enough.

I always add a molex plug just to make life easier, or if you want to use a different driver in the future. Speaking of plugs, now is a good time to cut off the plug end of your extension cord. Wire it (with caps or solder directly) to the AC end of the driver, which is blue (negative) and brown (line). The other end of the driver is the DC end, wire that to the other end of the molex plug. Here's the finished light ready for testing:

Want to test the connections? Put the multimeter in diode mode and touch each side. The LED will light up if the connections are good. Series circuits are like old Christmas tree lights: If one connection is bad, the whole thing won't light. Here's me testing a bigger light. It's good!
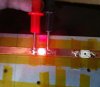
If the connections check out, plug it in! Be careful, it's super bright!!

That second pic is a flower light, complete with warm white and royal blue LEDs. It was built in much the same way, except using two drivers.
There you have it. Your own tiny LED light. It's not pretty, in fact it's pretty ghetto. But you built it, it will grow plants, and now you have the materials, knowledge, and manual dexterity to build more. Here are a couple fun shots of plants grown under these lights.
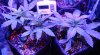
DIY LED lights are perfect for space-restricted micro cabs. They're small, customizable, efficient, and (best of all) COOL. No more overheating PC cases!
I made this light with leftover supplies from a much larger light. It was fun to assemble and took about an afternoon. The design is meant to be as cheap and efficient as possible. This light can be used standalone for micro grows, for vegetative and/or mother cabs, or to supplement specific areas of a larger garden. Build the light as pictured, or expand it over a larger heatsink. The basic concept is the same whether you have 4 or 40 LEDs.
Before embarking on this adventure, be advised that it helps to have soldering experience BUT it's not necessary. A beginner should watch a couple youtube tutorials, then practice soldering wires together until they get the hang of it. A basic knowledge of electrical concepts is helpful as well, although if you've ever wired a DC fan to a wall-wart it's really not much more complicated than that.
Without further ado, let's get started. Here we have our supplies (counter clockwise from top left):
Osram Golden Dragon Plus LEDs 660nm red and 6500K bright white (~$5-$7 each from Mouser, more if you buy in bulk). These have a nice, wide coverage angle (170 degrees) and are easy to solder. You can get the plants nice and close without burning them. For a flower light, 3500K warm whites should be used in place of 6500K; also add a royal blue if you have space. For flowering I use a ratio of 5R:2W:1B.
Pre-stripped wires (from Rapid LED)
Molex connector that I'll cut in half to use for the plugs (also from Rapid LED)
Meanwell LPC-35-700 driver Readily available and cheap (~$16) that will drive up to 48V of LEDs at 700mA. Features short circuit and overcurrent protection in the form of a xener diode. Basically they're rock-solid. One of these will drive up to 12-15 LEDs on average.
Wakefield thermal pads, 173-7 series (also available from Mouser, very cheap, very thin @ .007", great thermal conductivity)
Copper CPU heatsink Any finned heatsink (aluminum or copper) will do; check ebay for a wide variety of cheap ones. This one is just an old one I had lying around. The bigger the light, the bigger the heatsink needs to be. A good rule of thumb is 9 square inches of heatsink surface area per watt for actively cooled lights; and 27 square inches for passively cooled. If your heatsink is too small, the area beneath the LED will get too hot, and your light will be less efficient.
Kapton tape to isolate the leads from the heatsink (couple bucks from dealextreme)
Thermal adhesive 2 part epoxy, non-conductive. I use Arctic Silver.
Multimeter for testing
Soldering iron & solder
Scissors, exacto knife (or razor) and tweezers
Extension cord (not pictured) You'll need this for the plug, so you can wire up the AC end of the driver.
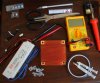
First we pre-tin the leads on all the LEDs and wires. This ensures a solid electrical path and makes connecting them to the wires much easier once they're mounted to the heatsink. Simply melt a bit of solder on the end of the gun and touch each lead for 3-5 seconds, or until the solder transfers over and becomes shiny. Go slow and be careful not to burn the plastic housing. After you tin, GENTLY bend the leads upwards a bit. This gives us more room to press the LED down onto the thermal pad in the next step. Pre-tin your wires as well.

Next, cut the thermal pads to size and glue them to the bottom of the heatsink with the thermal paste. Ideally they should be slightly larger than the metal slug at the bottom of the LED. Apply pressure while the epoxy sets up; about 5 minutes is enough. Once it's dry you can trim off the excess goo with a razor.
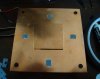
Put a small piece of Kapton tape on each side of the thermal pad. This electrically isolates the leads from the heatsink.
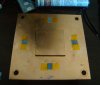
Dab a bit of epoxy on the top of the pad and attach the LED. Again, apply gentle yet firm pressure to the sides of the LED while it dries (about 5 minutes). If a LED comes off, scrape the dry glue from the bottom and re-apply. If the epoxy is stubborn, clean the area with alcohol and start over. Attach each LED with the cathode (negative) side facing the same way. See that little dot to the right of the light? That's the cathode side.
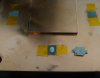
Once you've attached everything let it sit for awhile as the epoxy sets up. Within an hour or two the epoxy will be 90% hard and you won't be able to remove the LED without risking damage to it.
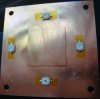
Almost there! Now we need to wire them together in series. Remember back in high school learning about AC/DC current, and parallel and series circuits? Well, LED lights are simply a series DC circuit. This is why it's important to keep the cathode facing the same direction. Since we pre-tinned all of our leads, this should be easy. Bend the wires where you want them to go, and touch the soldering iron to the leads, connecting positive to negative all the way around. They should adhere within seconds. Again, this is where your super excellent soldering skills will come in handy, so practice up a bit! As you can see, mine are not perfect, but it's good enough.

I always add a molex plug just to make life easier, or if you want to use a different driver in the future. Speaking of plugs, now is a good time to cut off the plug end of your extension cord. Wire it (with caps or solder directly) to the AC end of the driver, which is blue (negative) and brown (line). The other end of the driver is the DC end, wire that to the other end of the molex plug. Here's the finished light ready for testing:

Want to test the connections? Put the multimeter in diode mode and touch each side. The LED will light up if the connections are good. Series circuits are like old Christmas tree lights: If one connection is bad, the whole thing won't light. Here's me testing a bigger light. It's good!
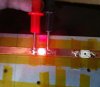
If the connections check out, plug it in! Be careful, it's super bright!!


That second pic is a flower light, complete with warm white and royal blue LEDs. It was built in much the same way, except using two drivers.
There you have it. Your own tiny LED light. It's not pretty, in fact it's pretty ghetto. But you built it, it will grow plants, and now you have the materials, knowledge, and manual dexterity to build more. Here are a couple fun shots of plants grown under these lights.

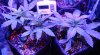